FONDAMENTA IN LEGA
La funzione e la struttura del basamento
di Roberto Maurelli
Una
vita da mediano. Così cantava Ligabue per celebrare il ruolo
fondamentale e mai abbastanza
riconosciuto dei centrocampisti, giocatori senza i quali
il buon funzionamento della squadra sarebbe seriamente compromesso.
Qualcosa del genere si potrebbe dire del basamento come
componente dei propulsori. Spesso trascurato nella descrizione
dell’architettura motoristica, è facile credere che si tratti di
qualcosa di facile da costruire nonché deputato esclusivamente ad
ospitare al suo interno gli organi del manovellismo. Ed invece così non
è.
Il basamento, infatti, oltre ad avere una geometria
complessa deve sopportare sollecitazioni incredibili, scaricate in
maniera repentina ad ogni giro dell’albero motore. Questo richiede che
la struttura debba essere estremamente robusta ma, dovendo fare i conti
anche con la leggerezza, mantenga anche un peso contenuto.
Contemporaneamente poi le geometrie devono consentire un adeguato
smaltimento del calore e limitare al massimo le emissioni acustiche.
Per avere un’idea basta pensare che in un moderno
turbodiesel ad alte prestazioni il picco di pressione durante la
combustione è nell’ordine dei 160 bar; questo significa che, se
l’alesaggio è di 80 mm, in un tempo estremamente ridotto ciascuna biella
scarica sul proprio cuscinetto una forza del’ordine di otto tonnellate.
Al fine di ottenere la massima rigidità complessiva e
facilitare i processi produttivi, generalmente il blocco cilindri,
oppure le bancate se il motore è a V, è incorporato nella stessa fusione
del basamento.
La soluzione con blocco cilindri amovibile, al contrario,
rende più rapidi gli interventi di manutenzione ma, oltre a peggiorare
la rigidità complessiva, comporta un leggero incremento di peso. In
genere questa soluzione è adottata quasi sempre quando i motori sono
raffreddati ad aria, come è accaduto per le Porsche del passato, per
alcuni mezzi popolarissimi come la Fiat 500, la Citroen 2 CV, il
Maggiolino, ecc.
Quanto ai materiali impiegati, per lungo tempo i
basamenti dei motori automobilistici sono stati realizzati in ghisa. Poi
la situazione si è modificata e, oggi, molti costruttori utilizzano
leghe leggere.
Per la verità, nei motori diesel, la situazione è molto
diversa poiché la ghisa la fa ancora da padrona per la sua attitudine a
smorzare le emissioni acustiche, assai critiche in motori di questo
tipo.
Non mancano neppure comunque realizzazioni nel prezioso
magnesio, impiegato da solo oppure combinato con l’alluminio.
Gran parte delle scelte costruttive in tema di basamento
devono tenere nella giusta considerazione l’alloggiamento degli altri
componenti, in particolare dell’albero motore. Non dimentichiamo,
infatti, che è nel basamento che viene collocato l’albero motore. Per
poter installare un albero a gomiti monolitico, ossia forgiato in un sol
pezzo, è necessario che i supporti di banco sui quali si appoggia siano
scomponibili. Ecco perché, quando si vuole adottare questa soluzione che
permette di conseguire una notevole rigidità, vengono previsti dei
cappelli scomponibili fissati ai supporti di banco attraverso due o
quattro viti.
Quando, invece, i supporti di banco non dispongono di
cappelli amovibili, si rende necessario un albero a gomiti che possa
essere inserito da un’estremità. Proprio per questo si dice che in
questo caso il basamento ha una struttura a tunnel. Nel tempo hanno
fatto ricorso a questa conformazione molti motori motociclistici, da
Guzzi a BMW.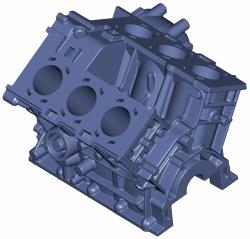
Certi basamenti sono costituiti da due parti che si
uniscono secondo un piano verticale mediano, che taglia a metà i
supporti di banco. Questa struttura è tipica dei motori a cilindri
orizzontali contrapposti e consente di ottenere una struttura molto
rigida. Un’altra soluzione poco consueta si ritrova oggi in alcuni
motori Porsche, nei quali viene impiegato un basamento esterno che ne
racchiude uno interno, nel quale sono ricavati i supporti di banco.
Questo schema costruttivo è funzionale essenzialmente a ridurre le
emissioni acustiche.
Roberto Maurelli |